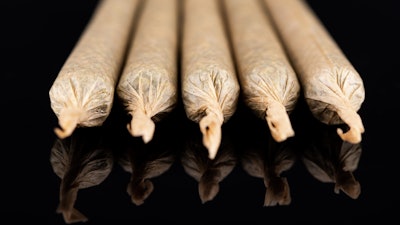
As the cannabis industry continues to grow, the pre-roll sector continues to lead the way as customers all over the country reach for the convenience and portability of pre-rolled joints. Not only are pre-rolls the industry's fastest-growing sector, but they are also the most popular add-on at dispensary check-outs.
So, it's no wonder that more and more companies are looking to be a part of this highly competitive marketplace. But while making pre-rolls is simple, making high-quality pre-rolls at scale is different. However, the right equipment and expert advice can de-mystify pre-roll production and have you dominating store shelves in no time.
As pre-roll experts, our team at Custom Cones USA has a full guide to pre-roll production, but today, we'll cover the best machinery and key steps used to produce high-quality pre-rolls.
Grinding & Sifting for Pre-Roll Production
As we always say, it all starts with the grind. Though it seems like the simplest step in the process, how you grind your flower can set you up for success or failure in the market, no matter what you do in the rest of the production flow. The wrong grinder can damage your cannabis, ruining its potency and flavor.
The most important thing to remember when grinding your cannabis is that machines that use a high-RPM, low-torque motor, like a blender, food processor or even whip-style shredders, produce a lot of heat and can destroy the valuable trichomes that contain the cannabinoids and terpenes that consumers are looking for in a quality pre-roll. Additionally, these "grinders" tend to turn your beautiful flower into dust in a matter of seconds.
According to our 2023 white paper on the pre-roll sector, some 23% of companies are still using a blender to grind their cannabis. That's not a recipe for success.
Instead, look for a machine like our Industrial Cannabis Grinder that uses high torque and low RPM to help break up flower. The grinder comes with three screen sizes, allowing you to control the particle size that comes out of the grinding chamber. The grinder also leaves stems intact so they can be sifted out. Shredder-style grinders obliterate stems, leaving them in your ground flower mix, which reduces the potency of the ground mix and makes it harsher due to the increased fiber content.
But before we get packing, let's look at the most overlooked aspect of pre-roll production: sifting. Sifting your ground cannabis will help further standardize your particle size while also removing seeds, bits of stem and other jagged pieces that can tear your pre-rolled cones during the process. Think of it as your first quality control step.
Sifting for pre-roll production.Custom Cones USA
Make sure you choose a sifter with changeable screens and screen sizes since different strains require different particle sizes.
This is all vitally important because consistent particle size is critical to producing well-packed, good-smoking joints that don't run or canoe, no matter what pre-roll filling machines you use. By sifting your ground flower to a more uniform particle size, your pre-roll machines will run more efficiently, metering trays will be more accurate, and you'll avoid issues like clogging or canoeing.
And yet, according to our research, only 40% of companies use a sifter in their production. Again, that leaves plenty of room for smarter companies to make better pre-rolls in a highly competitive marketplace.
Pre-Roll Cone Filling
Despite the early work, it's still not a pre-roll until you pack your cannabis into cones. It should go without saying that while there are plenty of options for size and paper type, choose a reputable company that tests their paper for pesticides, heavy metals and microbials to not only keep your customers safe but ensure your paper is as clean as your flower so you don't trip over any state-mandated tests or regulations.
With your pre-rolled cones selected, it's finally time to fill them. For most producers, it comes down to choosing the best machine to fit their filling needs.
The first choices a producer has to make when choosing a cone-filling machine are electronic versus non-electronic and tabletop versus fully automated. Non-electronic machines, like the Bumpbox or the Fast Fill series (which also can be used with an optional electronic vibration table), rely on a worker thumping the device up and down with their arms. The method is a great way to get started on a budget, but very labor-intensive.
On the other hand, an electric cone-filling machine uses either a series of vibrations or up-and-down motions to help the cannabis settle and pack into the pre-rolls evenly. Among electronic pre-roll filling machines, those with a bounce motion, like the King Kone machine, create a tighter pack than a vibrating platform or knockbox-style machine.
Electronic machines, while usually a more expensive investment, allow for quicker production runs, cut down on labor requirements and create a more consistently high-quality pre-roll by removing the possibility of user differences from cone to cone.
The King Kone machine provides a bit of both worlds. It is a tabletop machine that takes up very little room and includes an adjustable motor that provides the up-and-down bounce to pack up to 169 cones at a time. It is suitable for small and large manufacturers, as its modular design is very friendly for assembly line manufacturing processes.
The metal King Kone Pre-Rolled Cone Packing machine.Custom Cones USA
Another consideration when looking at pre-roll filling machines is the type of pre-rolled cone or tube you plan on filling. We found that 77% of companies fill cones, for example, while 8.2% use tubes and 14.8% make both shapes.
For example, King Kone comes with several attachments so that it can pack half-gram, 3/4 gram and 1-gram pre-rolled cones (by far the most popular size) right out of the box with no extra attachments required. But it is also versatile and can fill pre-roll tubes, too. Plus, its price point means that scaling up often just involves buying a second or third unit.
For companies looking for a larger production run, the thought is often "What machine is the biggest?" or "Which machine holds the largest number of cones?" However, the number of pre-rolls packed at once does not equate to a higher overall throughput. The bottleneck in the pre-roll manufacturing process occurs later downstream when it comes time to remove the pre-rolls from the machine, twist or fold the top, and package.
Our Fill and Fold pre-roll machine has a patented folding tool, which helps you tamp and add a Dutch-crown finish on all the pre-rolls in seconds.
The Fill and Fold tool with tamping and folding capabilities.Custom Cones USA
There are also fully automated pre-roll filling machines that can produce between 800 and 2,000 pre-roll joints per hour, a significant increase over tabletop machines. However, we don't usually recommend those until your company sells about 50,000 pre-rolls per month.
Additionally, there are many pros and cons to automating your pre-roll production, so consult with an expert before making such a large investment.
The Most Important Pre-Roll Decision You'll Make
Choosing the right pieces of pre-roll equipment to match your production needs isn't easy, especially given the ever-growing number of available options. That's why the most important choice of all is your pre-roll supplier. Make sure the company you are dealing with is an expert in not only the machinery and products they sell but also the cannabis industry and pre-roll market as a whole.
Whether you are just starting, scaling up or even trying to keep up with new trends like the spectacular growth in infused pre-roll sales, your supplier must have your best interests in mind.