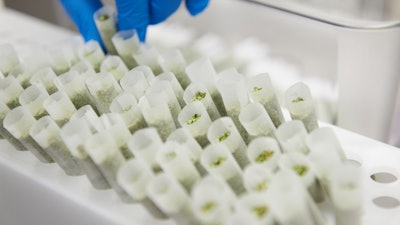
The cannabis industry is in a nearly constant state of flux. Dealing with regulations on the state and federal level amidst a changing environment puts these companies in a difficult position. Whether we’re talking about hemp, cannabidiol (CBD) or recreational marijuana, things in cannabis are complicated right now.
The 2018 Farm Bill might’ve added a bit of legitimacy to some cannabis companies, but the industry is having a hard time shedding a negative image. This is especially difficult in light of the recent vaping crisis. How do companies avoid similar problems in the future while preparing for regulations? Quality.
Most life sciences industries are regulated with the intent to protect consumers. And even though one cannot predict how the industry will be regulated, cannabis companies can learn a lot by looking at other regulated industries. For example, current good manufacturing practices (CGMPs) will probably come in to play and companies selling edibles will have to follow food manufacturing regulations. In all cases, following regulations requires stringent quality management, something companies can adopt and adapt even as the specifics remain unknown.
A Quality Organization
Most cannabis companies haven’t been in the business long. That might pose some challenges, but being a smaller, newer company can certainly be beneficial. This is especially true when it comes to quality. Quality is more than just a department. It needs to be an attitude that permeates the entire organization. The c-suite, manufacturing line, product development, etc. all need to have quality as a top priority. Employees should be “passionate about quality as a personal value rather than simply obeying an edict from on high.”1 Ideally, companies should have this attitude from their founding. However, that’s not always the case, which means an attitude shift is due in some businesses.
Bringing quality into an organization is limited when the focus is solely on regulations or standards because it turns quality management into a checklist. Unfortunately, this approach doesn’t necessarily improve quality. It’s possible to comply with a regulation or standard on paper while completely missing the mark on the reason behind it. To get everyone in a company concerned with quality, everyone needs to be involved with quality. This doesn’t mean every member of an organization needs to become a member of The American Society of Quality (ASQ), but leaders should encourage ideas for improvement from those outside of the quality department and recognize those contributions.
Larger companies may try to make this change, but it’s difficult in a well-established organization that has a “that’s how we’ve always done it” mentality. In a younger organization, “how we’ve always done it” might be a matter of only a few months’ or years’ worth of behavior, which is easier to change. Producing a quality product in a quality organization means that when regulations appear, a company won’t need to make as many changes to its procedures. A reputation for quality also increases a brand’s worth in the eyes of consumers. According to one expert, “attention to repeatable quality will go a long way to forging trust with regulators as well.”2
Get Prepared for Regulations & Inspections
As previously mentioned, regulations are coming and quality will help you prepare. Some good examples of this are found in well-established regulated industries. The pharmaceutical industry faces some of the most stringent regulations and the U.S. Food and Drug Administration (FDA) keeps a record of when companies fall short of those expectations.
One of the most common reasons that the FDA issues warning letters is a lack of data integrity. This can be a problem with omitted information, backdating record entries, disabling audit trails, and more.3 Making quality a part of your processes now saves trouble with regulatory bodies later.
Another advantage that smaller startups have over larger businesses is that most of them have always been digital. This eliminates the need to digitize and get rid of paper because it was never there in the first place. Cannabis companies are in a better position to ensure data integrity when they use digital systems. A quality management system (QMS) in particular keeps all your documentation in a centralized location. All training records, work instructions, bill of materials, etc. are easily accessible and any edits are tracked in the system. You can further ensure connectivity by using an electronic manufacturing system that digitizes your production records.
Protect Your Consumers
Quality is important not just because it improves how consumers perceive you, but also because it protects them. The recent vaping crisis highlighted the problems that untested additives can bring to the market. The problem that killed dozens and sent thousands more to the hospital was linked to vitamin E acetate, used in some THC vaping products. Most of the problematic products were illicit, but the incident still brought a renewed emphasis on the importance of testing products, vetting suppliers, and improving and monitoring production processes.4
Better quality management will lead to safer products. And since regulatory bodies are all about safety, better quality management also means you’ll be compliant. Ideally, quality management would let you completely avoid suppliers and ingredients that could pose a problem. While this would be nice, it’s not very realistic. When you encounter a quality event, the safety of your customers could depend on how you handle it.
If your corrective and preventive action (CAPA) process isn’t connected across sites, you might miss major red flags. One customer complaint by itself isn’t necessarily indicative of a bigger problem. However, if there are multiple complaints about the same product with the same problem, a CAPA is warranted. These kinds of problems are easy to miss if cannabis relies on outdated, siloed processes.
Increase ROI
One of the biggest obstacles to quality can be the expense. Especially if you want to bring a fully connected, automated system into the mix. It’s true that under traditional pricing models a QMS or any other enterprise software system could be extremely costly; not just in terms of licensing, but also in terms of the hardware required on-site. However, this is an outdated view of these solutions. Choosing a cloud-based system from a software as a service (SaaS) company saves you time and money. Not only do you not have to provide the same hardware, you can save on IT resources and your data will be more secure. Some SaaS companies even have subscriptions specifically for startups to help with the price.
These significantly lower prices might still seem beyond very young cannabis companies. However, any business endeavor requires investment, and, in this case, it doesn’t take long to recoup an investment in automation. In terms of time, money and frustration, automation pays off in a big way. Regardless of the approach to quality you take, the returns are huge. Startups have limited resources, which means your employees should be spending their time solving problems that need human intelligence. The reality is that many employees operating in this industry spend time on tasks that could be automated. Whether that’s getting approval on a document, collecting training records for an audit, or reviewing a production record before a batch is released, automation either eliminates or greatly reduces the need for human involvement in these processes. The American Society for Quality (ASQ) has some interesting stats on quality’s ROI. One study showed that for every dollar spent on quality, companies returned $6 in revenue, $16 in cost reduction, and $3 in profit.5
Conclusion
The cannabis industry might be young, but it’s growing fast. That kind of growth attracts entrepreneurs and means the industry is inundated with startups. As those startups see their initial investment turn into a much bigger investment and try to find ways to make the money stretch, it can be tempting to cut corners. Depending on which corners are being cut this may not be a problem, but quality is one area where spending extra now will protect the company later on.
Building quality into the company culture from the beginning paves the way for a compliant organization. Regulatory bodies are still working through what forms of cannabis are legal in their states and countries. In some cases, regulations have been slow to follow. If anything, this is an argument for stronger quality management as preparation for eventual regulation. While cannabis companies wait for regulations, they’ll enjoy higher customer loyalty, a better quality product, and significant ROI for their quality efforts.
Sources:
- Srinivasan, Ashwin and Kurey, Bryan. “Creating a Culture of Quality.” Harvard Business Review. April 2014. Retrieved from https://hbr.org/2014/04/creating-a-culture-of-quality
- Drotleff, Laura. “Consistency and Compliance Are Key to CBD Success.” Marijuana Business Magazine. February 2020. Retrieved from https://mjbizmagazine.com/digital-issues/2020-02-Feb/10/
- Jensen, Dave. “Surge of Data Integrity Violations Irritating the FDA.” GxP Lifeline. 12 December 2019. Retrieved from https://www.mastercontrol.com/gxp-lifeline/surge-of-data-integrity-violations-irritating-the-fda/
- Sacirbey, Omar. “After the Storm.” Marijuana Business Magazine. February 2020. Retrieved from https://mjbizmagazine.com/digital-issues/2020-02-Feb/44/
- American Society for Quality. “Making the Case for Quality.” Retrieved from http://asq.org/economic-case/