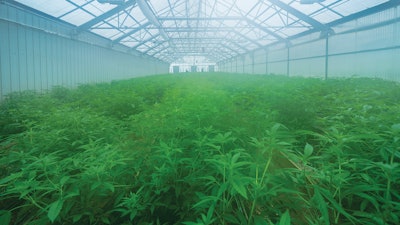
On the western slopes of Mesa County along the Colorado River is the city of Palisade. Known primarily for its fruit trees and vineyards, it holds the title “Peach Capital of Colorado,” but small farmers are increasingly dedicating acreage to the production of hemp in pursuit of higher profits.
With the legalization of hemp production in late 2018, and the demand for hemp-based products growing dramatically, many small farmers are considering the switch. “In 2017, we planted one acre of hemp,” says Chip Wernig of Palisade Farms, LLC. “In 2019, we planted 22 acres. That’s over 30,000 plants.
To keep pace with demand and maximize production during harvest seasons, Wernig recently purchased a greenhouse where the seedlings can be started ahead of planting. He also upgraded his processing operation with a BEV-CON flexible screw conveyor from Bethlehem, Pennsylvania-based Flexicon Corporation as well as a new dryer to process hemp biomass (view photos in gallery).
Minimizing harvest-to-baling time
The plants are harvested manually and fed into bucking machines that separate the flowers, leaves and seeds from the stems.
The de-stemmed material, known as hemp biomass, discharges onto a conveyor belt that moves it to a shredding machine and then to a dryer. Hemp is traditionally air dried slowly by hanging the plants upside-down, similar to drying of tobacco, but Wernig reduces drying times to 72 hours or less using an industrial dryer.
Conveying fragile flowers, seeds and leaves gently
The dried biomass is transferred via belt conveyor to the hopper of a flexible screw conveyor. At the hopper’s outlet is a U-shaped charging adapter in which the lower end of the flexible screw is exposed, charging the conveyor with material.
Biomass is discharged from the flexible screw conveyor into a wye diverter, which feeds two balers.Palisade Farms
The BEV-CON model utilizes a flexible screw having specialized geometry, and was specifically selected to gently transport fragile flowers, seeds and leaves. As the flexible spiral rotates, it self-centers within the tube, which propels material through the tube while minimizing crushing and grinding action.
At a height of 15 ft (4.5 m), the biomass is discharged into a wye-diverter leading to either of two baling machines that ready the material for shipping to processors.
The spiral is the only moving part contacting the material, and is driven by an electric motor beyond the material discharge point, preventing product contact with seals or bearings.
“This is a brand-new process for us,” Wernig explains. “Before, we were using an old hops dryer that we had purchased from a European harvester, and a much slower conveyor. Back then, we could process 700 to 800 pounds (315-360 kg) of hemp into product per day. With the new dryer and BEV-CON conveyor, we now do that in an hour.”
Bales of hemp awaiting shipment to processors.Palisade Farms