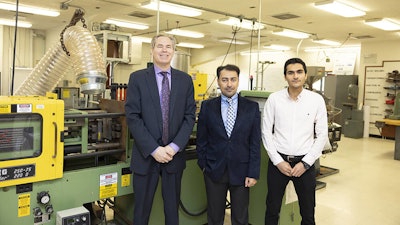
Engineering Technology Assistant Professor Mahdi Vaezi is leading a team of NIU researchers who hope to find a more environmentally friendly way to make plastics by using a plant that’s well known these days for its recreational purposes: cannabis.
Plastic products can take centuries to degrade, and more than 9 billion tons of plastic have been made since the 1950s. The vast majority of it has been tossed in the garbage. In addition, by 2040, greenhouse gas emissions associated with manufacturing, use and disposal of traditional fossil fuel-based plastics are expected to account for 19% of the global carbon budget.
With funding support from RYMAC Industries, LLC, Vaezi and his team are seeking to replace a portion of plastic in plastic products with biodegradable composite materials. To accomplish this, the researchers will mix traditional plastics with cannabis—or more specifically, the fibers of industrial hemp (Cannabis sativa).
“Depending on the source of plastic, whether natural or petroleum-based, our bio-composite products will degrade much faster than ordinary plastics,” said Vaezi, whose research specialties include waste management. “Furthermore, they will be greener than pure plastics because the manufacturing process will require smaller quantities of fossil fuels.”
Hemp and marijuana are both varieties of cannabis, but the difference is found in their psychoactive component: tetrahydrocannabinol (THC). The amount of THC in hemp is so small that it is of no use to the recreational marijuana industry (although it can be used for CBD extraction).
For decades, federal law did not differentiate hemp from other cannabis plants, all of which were effectively made illegal in 1937 under the Marihuana Tax Act. It made it difficult to study uses for the plant, but federal farm bills in 2014 and 2018 created protections for hemp research.
With its lightweight and strong fibers, hemp has been used for thousands of years to make rope and fabric. The fast growing flowering herb also sucks up carbon quicker than most other plants—twice as fast as a forest. For that reason, some hemp proponents believe carbon credits for hemp fields could be on the horizon.
Attorney Ryan McQueeney, a former dispensary owner, founded RYMAC Industries for the purpose of exploring hemp use in plastics, using stalks of the crop. He sees lots of potential.
“The cannabis industry now is kind of like being in the oil industry in 1890 or the car industry in the early 1900s,” McQueeney said.
“If we could, let’s say for example, end up with a process that can make plastic utensils . . . we’d be creating another crop in Illinois with value, capturing carbon in natural way and creating a new industry for processing and manufacturing in the state.”
Plastics is a $600 billion annual business and the sixth largest industry in the United States, according to the Plastics Industry Association.
Using industrial hemp to create various products, even automobiles, is not a new idea. The basic building blocks of plastic are large molecules called polymers, typically manufactured from petroleum sources. But petroleum-based plastics require drilling and mining of materials, an energy-intensive process that generates pollution.
Hemp, on the other hand, is a resource that can be quickly renewed in a more environmentally friendly manner, and the plant also can be used to make biocomposites.
Vaezi, together with Engineering Technology Professor Robert Tatara, who oversees NIU’s plastics lab in Still Gym at NIU, first conducted a feasibility study for McQueeney, pulling in information from previous studies of hemp-based plastics. As they embark on the second phase of the project, the researchers are teaming up with Mechanical Engineering Assistant Professor Sahar Vahabzadeh and research assistant Mohammad Faghani.
The aim is to come up with the ideal recipes and processes for plastic materials made with hemp additives.
“By adding a natural component that tends to absorb water, that should improve degradation (of the plastic products) or recyclability,” Tatara said. “But those qualities also will depend somewhat on what plastics are in the mix. We’re going to be trying different types of plastic, with the intent of creating an eco-friendly and viable product. There is always a need for better composites and for composites you can ultimately recycle.”
The effort is a complex engineering undertaking. It involves determining the percentage of hemp to use in their plastics and manufacturing variables such as optimal moisture control, production temperatures and mechanical processing methods. Different materials and compounds can produce different plastic qualities, such as high strength, low density and sound absorption.
“I couldn’t speak more highly about the experience of doing this with NIU,” McQueeney said. “They’ve been spending time educating me, too, and being open minded and available.”
Once the processes are optimized, the engineering team will produce three categories of materials that can be used to build products: plastic ingots for machining applications, pellets for manufacturing purposes and filaments for 3D printing. Each raw product will likely have its own recipe, since each has different desired properties.
“If we can achieve 40 to 60% of hemp (in the plastics), it would be that much more environmentally friendly,” McQueeney said.
The researchers also will be working to find the best and most cost-efficient methods for producing their products, which will be tested for strength, durability and other properties.
“It has to be something that makes financial sense,” McQueeney added. “I told them, ‘I want you to go in there and be mad scientists.’ I want to get the smart guys in a lab, let them work and maybe we’ll get a eureka moment out of it.”