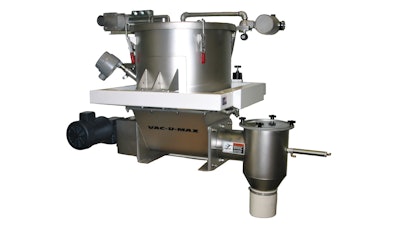
Vacuum conveyors that transfer dry solid and bulk powder materials reduce labor costs, streamline production processes, improve quality, eliminate waste, and prevent dust from entering the environment which poses costly health and safety risks.
Cannabis and hemp processing facilities, including edible and infused beverage manufacturers, CBD tablet and capsule producers, white label processors, toll processors, and seed-to-shelf facilities, can increase margins by implementing proven vacuum conveyor technology to automate dry bulk material and powder transfer from once process machine to the next.
Vacuum Conveying (aka pneumatic conveying) is the gentle automated transfer of dry bulk materials and powders from place to place within a facility, using suction, through a tubing network.
Vacuum conveying systems are fairly simple and consist of five basic parts: a pickup point where material enters into the conveying system; convey tubing that transfers material between equipment; a vacuum receiver (aka filter receiver), which is an intermediate holding vessel for materials; a vacuum source that powers the system; and a control panel that tells the system how to operate.
In addition to reducing manual labor costs, vacuum conveyors mitigate dust and safety hazards that manual scooping and dumping pose, preserve and capture materials for reuse and recycling, and deliver ingredients with precision measurement to boost quality and ensure consistent dosing.
Much like expert cannabis and hemp cultivators and processors possess deep industry knowledge, expert conveyor manufacturers that have worked with over 10,000 materials, covering nearly every industry that deals with powder and bulk materials, have a special type of tribal knowledge that transcends computer programs, making material transfer more of an art than a science.
This tribal knowledge of powder or dry bulk materials’ characteristics, coupled with application experience, facilitates the adaptation of equipment to fit proprietary needs of processors and the ability to adopt solutions from different industries that use completely different materials, but which have similar material characteristics and conveying challenges.
Below are some examples of how cannabis and hemp producers’ high purity “cousin” industries (food, pharmaceutical, nutraceutical and cosmetic) utilize FDA and USDA approved sanitary design vacuum conveying technology to increase their bottom line and improve safety.
Filling and Refilling Packaging Machines and Feeders
Packaging machines and feeders are often purchased without considering how they will be filled and refilled. Vacuum conveying offers the fastest (usually in a matter of seconds) and safest way to refill auger fillers, volumetric and gravimetric feeders, vertical form fill seal packaging machines as well as tin and stick fillers.
Multi Ingredient Batch-Weighing
Multi-ingredient batch-weighing hopper feed systems convey major, minor, or micro ingredients, such as powders, granular food ingredients, nuts, and other bulk ingredients, that allow minimal product degradation when pneumatically conveyed.
Topping Spreader Feeders
Spreader feeders automatically reclaim and reuse excess toppings—sugar, salt, sesame seeds, cornmeal, chopped nuts, and more—that drop from conveyor belts and convey them back into topping machines for even redistribution.
Tablet Fillers and Gel Capsules Transfer
Ready-to-operate vacuum tablet press loaders are available as complete systems for mounting on single or dual hopper tablet presses.
Gel cap and capsule conveyors are turnkey systems engineered for easy transfer of gelatin, liquid-filled and split capsules, to counting, polishing, inspection, weighing, filling, and packaging stations.
Mobile and Column Lift Conveyors
Mobile and column lift conveyors are complete conveying systems that raise and lower the vacuum receiver in order to load taller equipment such as mixers, reactors and other processing equipment with hatch doors and then bring the vacuum receivers back down to ground level for cleaning or sanitizing--eliminating the need for stair climbing.
Direct Charge Blender Loading
Direct charge blender loading is a unique adaptation of vacuum transfer using vacuum tight process vessels, such as blenders, as the primary vacuum receiver for material being charged into it. These systems significantly reduce the amount of carry over, eliminating product loss and ensuring batch integrity.
As the cannabis and hemp industries grow, the number of unique vacuum conveying applications will also grow. These are exciting times.
For more information, visit www.vac-u-max.com.