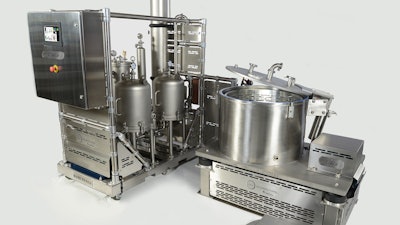
Cannabis automation has helped growers, manufacturers, and retailers reduce operating costs, maintain consistency and quality in products, and increase workplace safety. Industry 4.0 technologies such as automation, artificial intelligence, the Internet of Things (IoT), big data, and machine learning are revolutionizing the cannabis industry.
Cannabis extraction systems that operate under extreme temperatures using highly flammable and explosive chemicals require strict adherence to safety protocols. Automation and data gathering in the extraction workflow can keep extraction techs out of the booth and focused on moving the business forward.
How Automated Systems Improve Safety in the Workplace
Preventing and controlling workplace hazards requires a holistic approach covering all available options for managing risks. Based on the Occupational Safety and Health Administration’s (OSHA’s) Hierarchy of Safety Controls, automation effectively addresses a variety of control options throughout the entire extraction process. Automation equipment controls every step of the process to reduce operator error.
In manual-operated equipment, extraction technicians must monitor pumps, valves, and other controls throughout the process. Automation technology controls all of these functions on its own, removing the tech out of the extraction room. Overall, automation reduces the variability created by manual operation and produces a pure and consistent product every time.
Elimination
At the highest level of OSHA’s hierarchy of controls, eliminating the hazard can involve isolating the extraction techs from the hazardous area. Most equipment requires operators to remain in the extraction booth the entire time. With automation, you can take techs out of the booth and control the equipment remotely on your phone or a control panel.
Automated extraction equipment removes the risk of accidents or injury during the most critical stages and allows operators to monitor the process and make adjustments from any location.
Engineering Controls
In a fully automated environment, engineering controls such as emergency stop switches, extraction booth interlocks, and control system limits significantly reduce serious workplace accidents. Automated machines provide real-time monitoring to keep operators aware of potential issues before they happen.
Emergency stop switches allow extraction technicians to press a single button and ultimately stop the system. For example, in the event of a vapor leak, operators can control the situation from the outside without putting themselves in danger.
Extraction booth interlocks are electrical signals going between the booth and the equipment. If the system detects an abnormality such as ventilation issues or hazardous vapor levels in the room, the system will automatically isolate the problem to create a safe environment.
Control system limits like Luna Technology's proprietary software monitor the pressure and temperature throughout the process. If the automated system notices any fluctuations that do not follow the “recipe,” it can stop that part of the process or shut the entire system down and alert the operator.
Safety alarms can be paired with automated controls to detect potentially dangerous gas levels and shut down the extraction system. When working with ethanol or hydrocarbon solvents, proper ventilation and gas detection are critical to providing a safe working environment.
Administrative & Work Practice Controls
Manual extraction systems rely on administrative and work practice controls. These control options include how employees perform their tasks. For instance, an operator would have to manually handle the equipment if the pressure in the system was rising too quickly.
Automated processes remove the operator during the production process, so all they have to do is load and unload the material and pour the oil.
PPE
Personal protective equipment (PPE) is at the bottom of the list of safety controls since it is not very effective at reducing risks of solvent extraction. Still, wearing the proper PPE improves employee safety even in an automated extraction environment.
Benefits of Safety in the Workplace Through Automation
Beyond keeping workers safe, automation benefits cannabis companies looking to stay ahead of the game.
Improved Morale
Automation removes much of the manual labor involved with extraction jobs. Workers are less tired, more energized, and able to engage their minds instead of performing repetitive tasks. As a result, techs have more time to handle more complex issues without spending more time in a higher-risk environment.
Reduced Costs
While some automated systems may require a more significant upfront investment, they also reduce the cost of operating expenses because they do not require several years of technical experience like manual extractions processes require. New employees are easily trained on automated extraction much quicker, allowing owners/operators to train multiple employees to oversee the operations.
Automation also reduces the risk of human error, often leading to expensive losses in the product. For example, if a technician makes a mistake when operating the valves, it can ruin an entire batch. In a high throughput environment, one batch can add up to tens of thousands of dollars in lost revenue.
Increased Efficiency
Automated extraction systems can provide higher efficiency with no bottlenecks. Automation creates a seamless workflow that transports material from one part of the process to the next. A series of pumps move the oil through the system, reducing product loss from residual buildup in the product containers.
IoT-enabled systems allow technicians to remotely monitor all stages of production. Remote monitoring can improve overall operational efficiency. Automation provides the highest data gathering to improve processes and reduce accidents, leading to downtime and reduced throughput.
Increased Competitive Advantage
Automated safety systems enable companies to record data and monitor small changes in temperature and pressures that affect the end product Automation allows companies to use the precise parameters on every batch to create a consistent and scalable product. Automation is the competitive advantage facilities need to grow operations.
Do Not Rely on Automation – Steps to Ensure Worker Safety
Automation technology is just one part of the many safety measures cannabis extraction facilities should employ. Even with the best-automated systems, accidents and injuries can happen, so workplace safety should always be top of mind. Safety first!
Tech Training
While automated systems are a big help when monitoring extraction processes, they still require a talented and trained operator to use the equipment and troubleshoot safety issues when they arise. Companies should properly train employees to use these new systems and reduce hazardous situations.
Regular Maintenance
It is essential to perform regular care and maintenance to keep your system’s performance and throughput high. Safety automation software can also provide updates during off-peak hours to avoid disrupting operations.
Lockout/Tagout
When servicing or maintaining pressurized extraction equipment, it is recommended operators follow lockout/tagout practices. Lockout/Tagout protects employees from unexpected energizing of equipment or the release of hazardous energy.
This procedure requires operators to turn off the machinery from its energy sources before performing maintenance and either lock or tag the energy-isolating devices. In some cases, this procedure may not be able to be completed since power must remain on for software and programming updates.
Risk Assessments
Knowing the risks involved with extraction processes that involve flammable liquids and gasses is essential to set up proper safeguards in the workplace. Automated machinery does not replace appropriate risk assessment of chemicals and procedures.
While there are other methods of extraction that can reduce the risk of working with flammable solvents, these methods compromise on quality and terpene concentrations and produce a lower-value product. Automated hydrocarbon systems can provide operators with a safe and innovative solution that does not sacrifice quality.
Regulation Compliance
Safety regulations are available for workplaces in the cannabis industry. Carefully review the rules with all employees and stay up-to-date with any changes in the laws. As federal legalization gets closer than ever, cannabis companies will need to maintain the highest level of safety compliance to remain active.
Automation technology does not eliminate the risk of workplace accidents and injuries but plays a significant role in reducing accidents. Operators looking toward the future should strongly consider upgrading to automated extraction solutions that will stand the test of time and meet consumer demand.