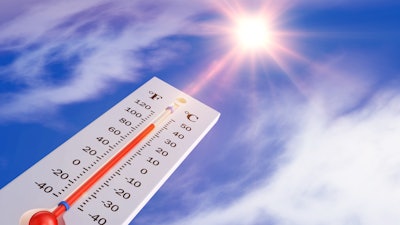
Summer is in full swing and that means some manufacturing employees are working in extreme heat, relying only on open windows/doors and fans for cooling. With this summer forecasted to be hotter than average across much of the U.S. (according to The Weather Company) and heat waves already occurring in the Midwest and South, heat safety is a major concern for the industry.
Manufacturing workers are not typically subject to direct sunlight, but they can suffer heat strain due to their own metabolic heat load, which is magnified when air temperatures are high. Without air movement, it is more difficult to cool off. Even with proper cooling, dehydration and heat cramps are possible if employees are not given adequate fluid replenishment and rest breaks.
It’s crucial for managers and supervisors to clearly understand the issues associated with extreme heat and develop a plan to minimize risks. Doing this can help prevent injury, heat strain, heat stress and other problems. Here are 10 ways manufacturing employers can ensure their workers are safe and productive while working in the heat:
- Know the signs of heat-related illnesses and how to respond. If something happens to an employee, it is important that you can recognize it and act accordingly. Your employees should also be trained to identify the symptoms in themselves and each other.
- Monitor the heat index each day and plan accordingly. The Occupational Safety and Health Administration (OSHA) recommends utilizing the heat index as a screening tool. The heat index uses actual air temperature and relative humidity to measure how hot it feels.
- Make sure your facility is properly ventilated. It may be difficult to ventilate the whole space in a large facility, but using portable fans, ceiling fans, and exhaust fans will help create air flow. Dehumidifiers can also help to keep conditions cool.
- Insulate hot pipes. A hot summer day can feel even hotter when heat radiates off pipes in a facility. Insulating exposed pipes will help cool the environment.
- Make sure equipment is working properly and not overheating. This will reduce overall heat build-up in a facility and could prevent bigger problems.
- Encourage rest breaks. It may seem like less work will get done, but if exhaustion or other heat problems set in, no work will get done.
- Ask how workers are feeling. Sometimes employees may feel uncomfortable approaching managers with issues, and they may also have health conditions which could exacerbate a situation. Keep their health in your top interests and ask them how they’re feeling. Consider using wearable devices, which are becoming increasingly popular, to monitor stress, exhaustion, humidity and the temperature.
- Offer hydration stations/water coolers, and make sure your staff knows where they are. Heat can cause dehydration.
- Encourage employees to choose their worktime meals wisely. Eating a high calorie meal can affect the body negatively when working in extreme heat.
- Remember normal safety routines. Don’t let the extra precautions for heat distract from the regular safety practices that keep workers healthy and safe every day.
As part of a heat management program, companies can also take measurements of employee heart rates, body weights, and temperatures that can provide better decisions about heat control. Heat safety in the workplace should never be taken lightly. Employers should look closely at the plans they have in place to help ensure their workers are safe, are able to perform their jobs effectively, and don’t miss out on summer fun.
Guy Stevens is a Senior Loss Control Specialist at QBE North America.